Filigrain, a piece of art made of (silver) threads …
In modern times, filigrain is a special form of jewellery technique, where fine wire (gold and/or silver) is used in jewellery.

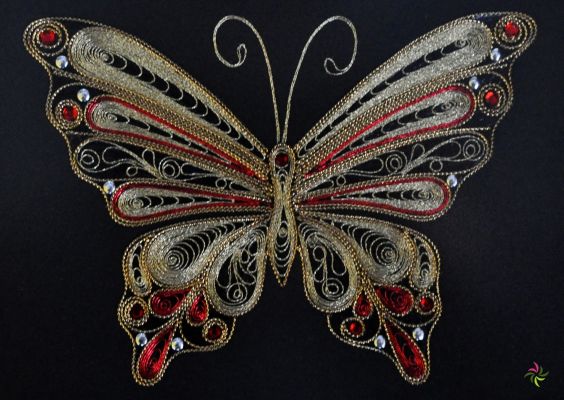
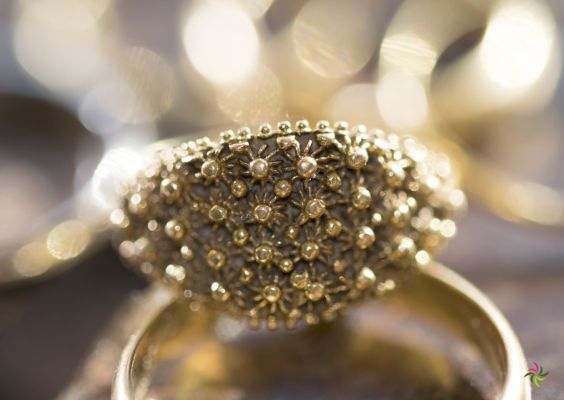
This involves very fine wire which is twisted or twined and which may be supplemented by small metal balls. All this is soldered together in various shapes and figures to create a beautiful piece of jewellery. It looks a bit like lace, but instead of cotton thread, it is silver or gold thread.
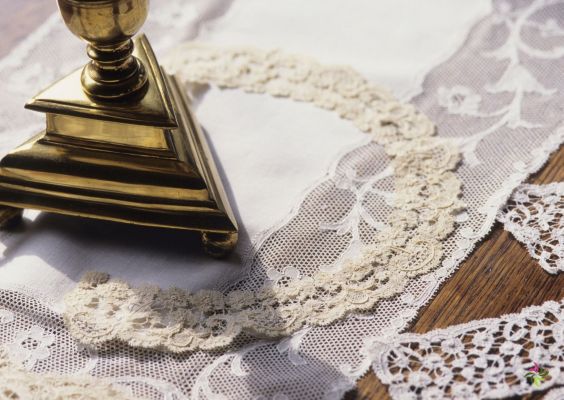
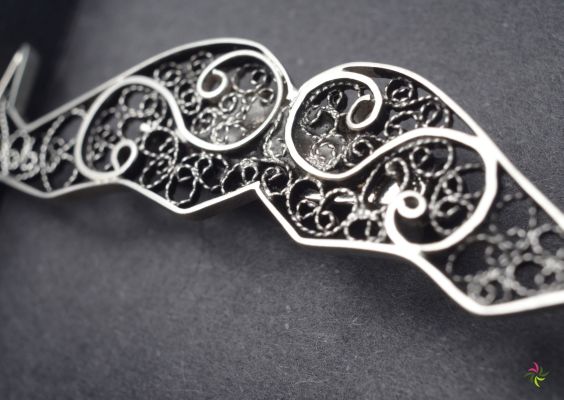
The name filigree comes from the Latin words “filum” meaning “wire” and “granum” meaning “small bead”. In Italian it then becomes “filigrana” and in French “filigrane” (17th century).
The technique has been used from ancient Egyptian, Etruscan, Greek and Byzantine times until today.
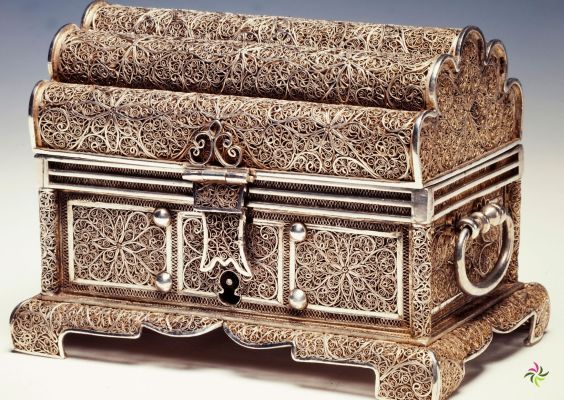
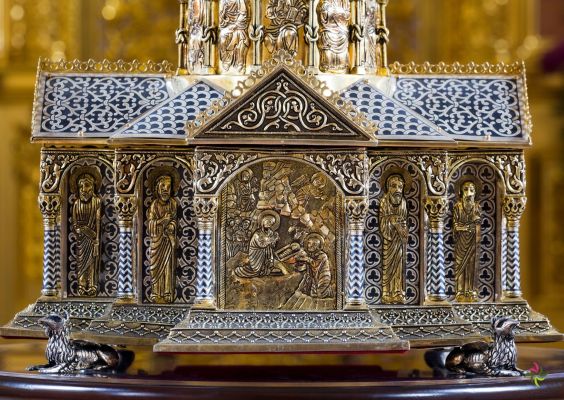
In the past and still today, some countries make beautiful and admirable pieces with many variations. Greek filigree is recognisable by different thicknesses of wire alternating with larger and smaller ornaments and beads, such as turquoise. In Portugal around the 8th century, under the influence of Arab migrants, new patterns were created and further perfected there.
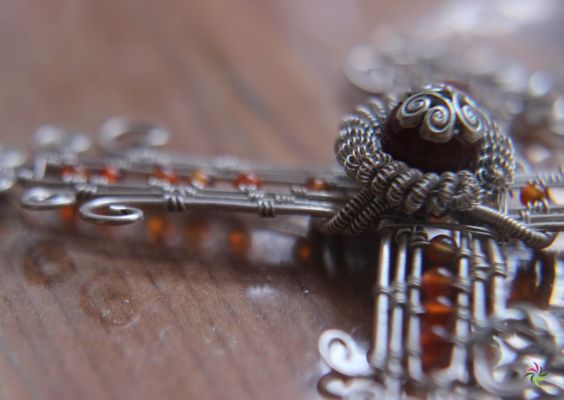
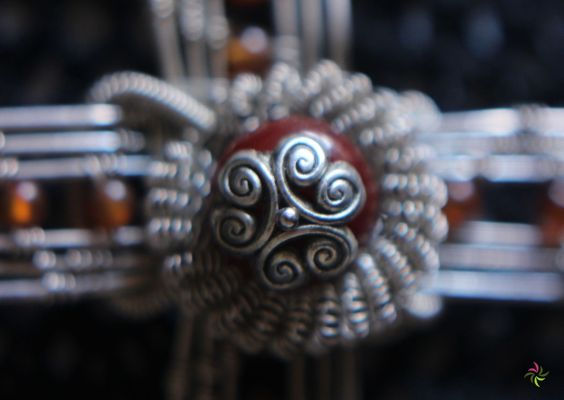
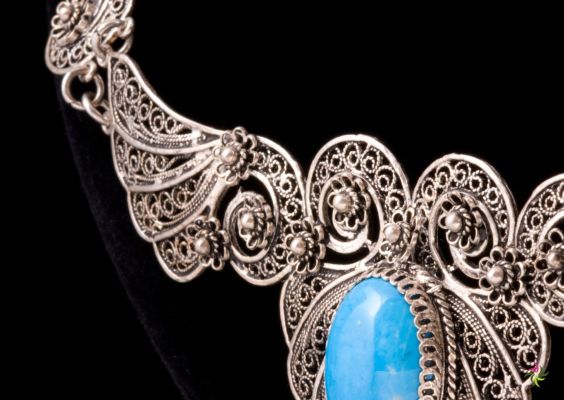
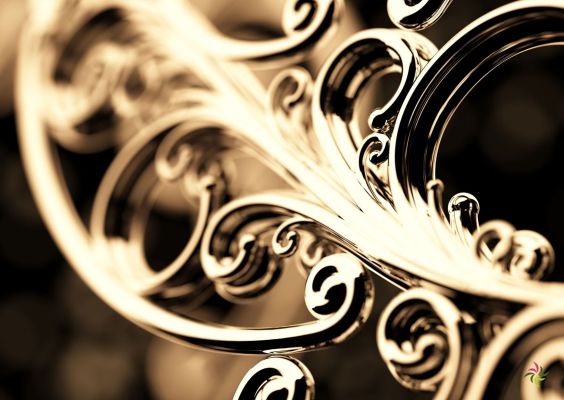
In some countries, it is a very popular technique, such as Asia (India), Russia, Hungary, Norway, Malta … but you can also find it in Italy, France and Portugal from 1660 until the end of the 19th century.
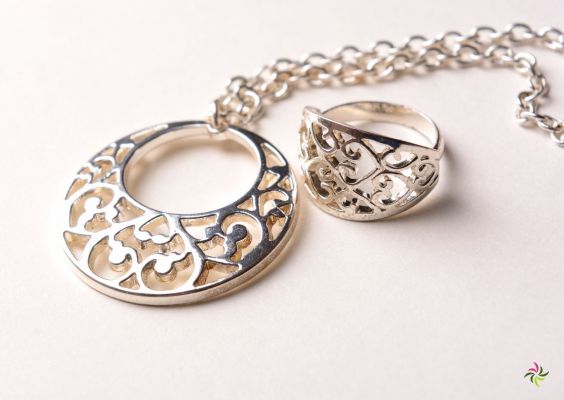
Do not confuse the technique with ajour. Ajour means sawing open shapes out of your metal.
Where a filigree jewel stands for very thin, fine wire work whether or not supplemented with balls, which also requires a special soldering technique.
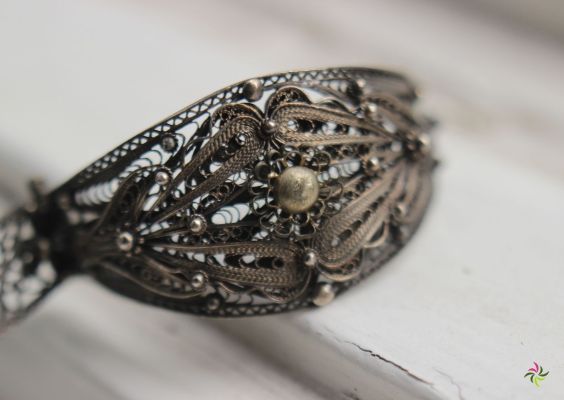

It is very inspiring and a real challenge to see how this technique was used in the past and how, even with more primitive means, they made beautiful jewellery and/or wirework from it.
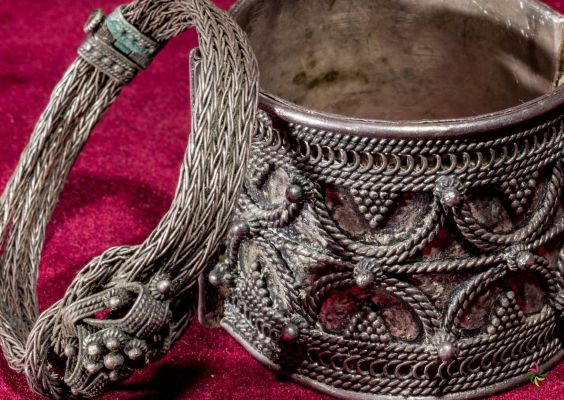
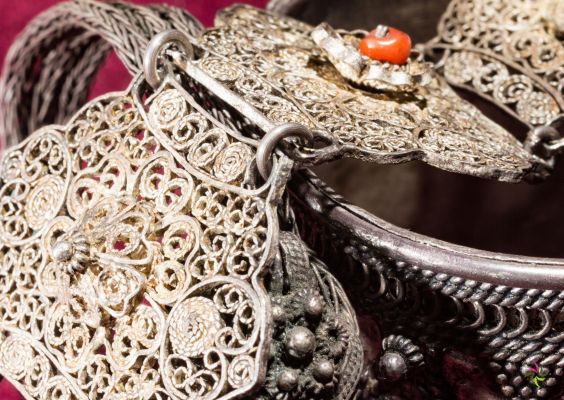
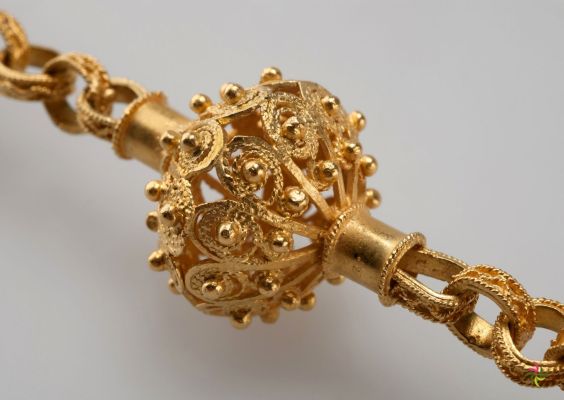
Basically, the basis of filigree work is always linear. The forms used are drop shapes, circles, ovals, spirals, curls, balls … These are joined together to form a larger whole or form. You can base yourself here on the shape of a flower with its petals or a butterfly with its wings. Thicker threads are usually used for the basic shapes and inside come the thinner inlay threads, which you will use alternately in different shapes. The flat surface can then be made spherical if desired. It is a very patient job, and is built up step by step from very small parts to a larger, beautiful whole.
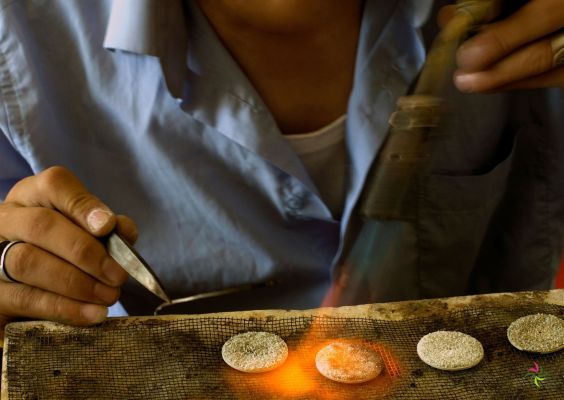

To preserve the traditional appearance of filigree inlays, it is important to maintain the correct proportions, i.e. for the (main) forms, the frame must be made using a wire that is 4 times thicker or wider than the inlays. We work with wire from 0.3 mm to a maximum of 1 mm thick. Naturally, by using the different thicknesses of wire the silversmith gives a personal touch to the design.

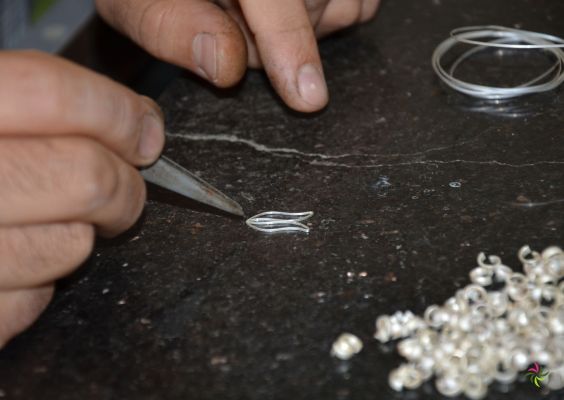
For the soldering of the wire, very small miniature peons (solder) are used (hard, medium and soft), but also what we call russet solder, which actually means ground or pulverised solder that you spread on your work using, for example, a salt shaker.
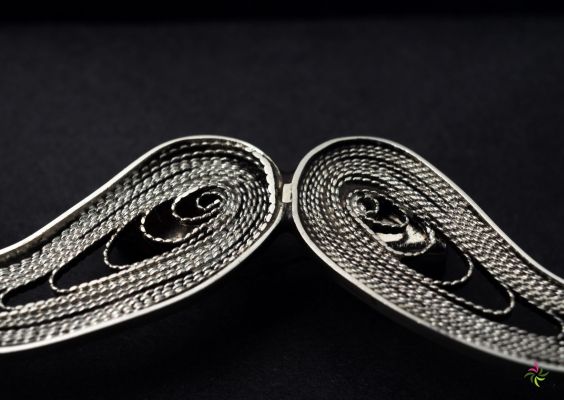
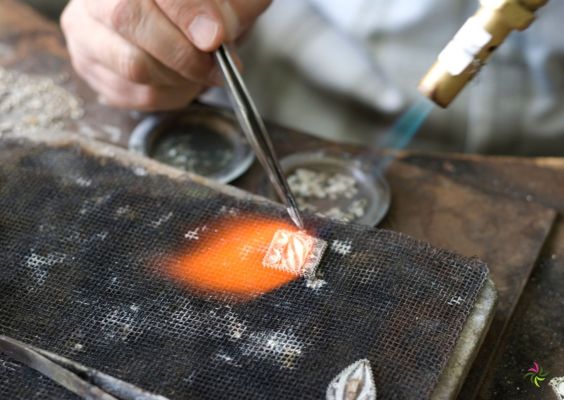
A magnifying glass or loupe, our fingers and hands are used here along with a pair of very fine bending pliers, fine tweezers and some bending jigs and other forming material to put together the very fine and small work.
Different variations can be used from open work, is an airy version, where no background is used. Or with a background, the main form then consists of a plate, which makes the form somewhat more solid. The inlay or wire patterns must prevail over the plate here. You can also work with a combination of open work and a background, or last but not least, you can work with an open form and add another material, filling the gaps with enamel or uv-resin, whether or not partially. The latter is mainly intended to add colour to the whole.
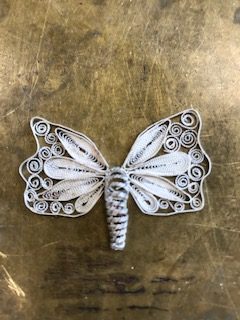
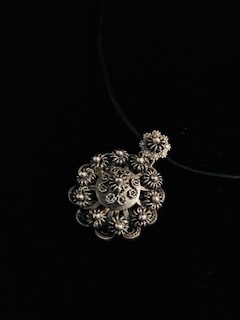
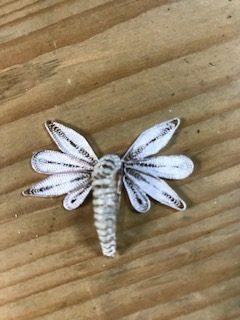
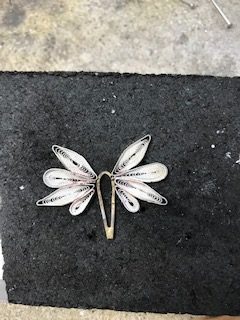
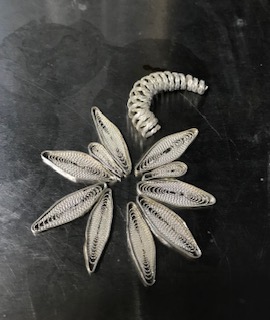
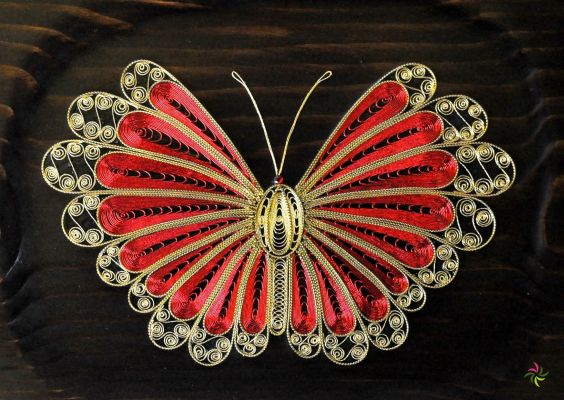
Silver of grade 925 is used for the silver wire work, and grade 750 (18kt) for the gold wire work. The silver often gets a very nice white colour, because the jewellery is regularly soldered in small pieces and put into the boiling acid. Gold, on the other hand, retains its shine better during frequent soldering.
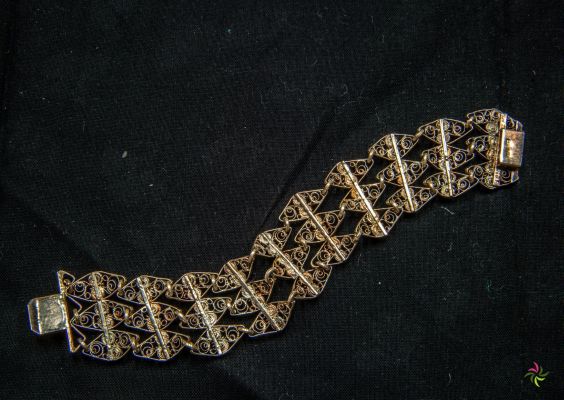
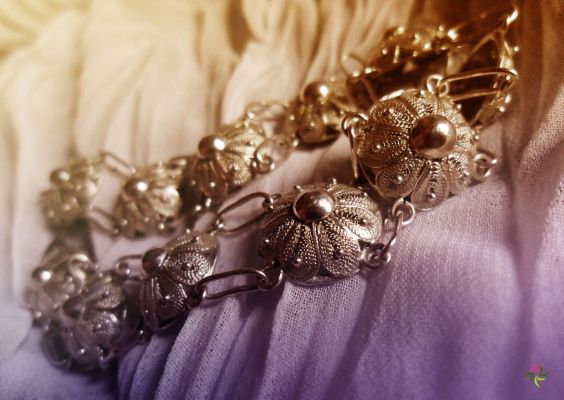
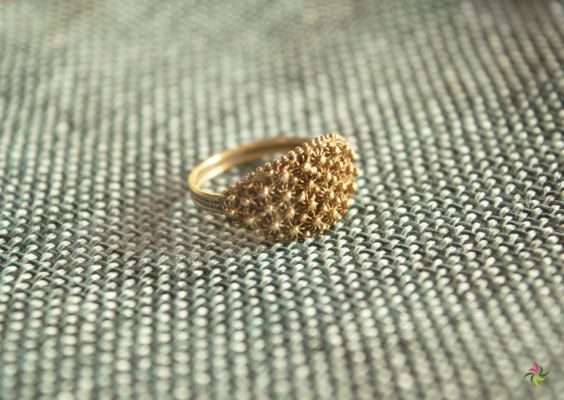
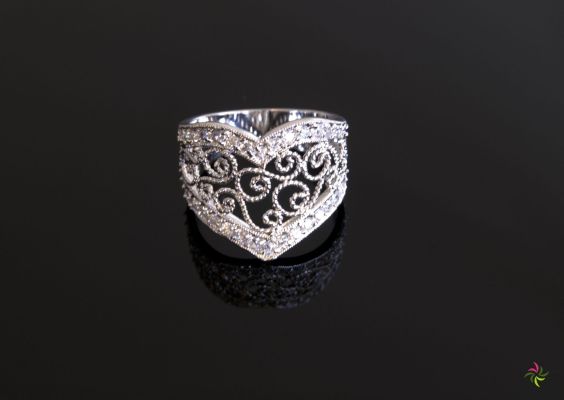
The final polishing of your “filigrain jewelry” is done using a soft brush and a mixture of chalk and fire spirit. If you want to give it a more old-fashioned look afterwards, you can stain it with blitz stain.
With other jewels, the polisher takes care of your ultimate shine, but this is out of the question with filigree jewellery because it is a fragile piece of wire inlay.
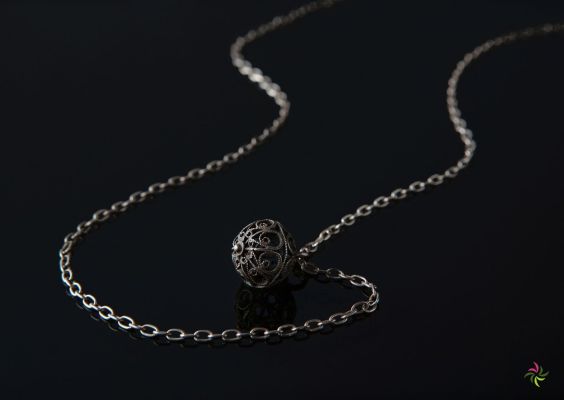
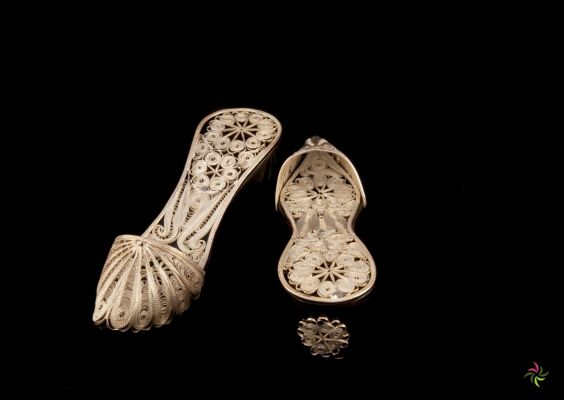
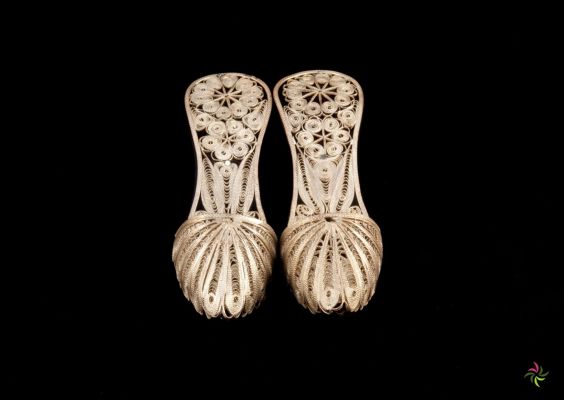